About Sintered Neodymium
Driven by the high cost of samarium cobalt magnets, the NdFeB Compound was first discovered in 1982. Neodymium magnets are the strongest type of permanent magnet commercially available, today. Yunsheng sells only patented, Hitachi-licensed sintered neodymium magnets. Neodymium has excellent characteristics: it has very high remanence and coercivity. It is possible to manufacture in a variety of shapes including radially-oriented magnets. Previously, at higher temperatures, only samarium cobalt was able to meet certain requirements. With the development of modern neodymium grades, some high temperature grades are able to exceed acceptable samarium cobalt temperatures. However, for most high temperature applications, samarium cobalt is still used based on a lower cost. Nevertheless, Neodymium is still one of the most widely used magnetic materials, today, because of its versatility, strong magnetic capability, and small relative size.
Process Control
A powder metallurgy process is used to create sintered neodymium magnets. As is true of other magnets, it should not be used as a structural component. Neodymium is prone to corrosion, requiring an outer coating or plating. Typically, a nickel-copper-nickel or epoxy coating is the plating of choice. Other coatings are available, if required. As the sintered neodymium is being manufactured in a Nitrogen-infused vacuum, any air particles (particularly oxygen) will allow the magnet to corrode from the inside out. All Yunsheng products are held to particularly rigid quality standards to control oxygen content and porosity. Patented processes are used to produce high quality magnets which are built to last.
Temperature Characteristics
Neodymium magnets typically have a higher temperature coefficient than other rare earth magnets. When the magnet is exposed to a higher temperature, it may lose part or all of its magnetic performance. Depending on the temperature and duration to which a magnet is subjected to, magnetic loss can be reversible. The recommended maximum operating temperature, residual induction (Br), and the intrinsic coercive force (Hci) should be considered when determining which magnet grade to use for your application. Contact your Yunsheng representative to find out the correct magnet for your application.
Applications include electronic, industrial, automotive, medical, as well as wind power solutions.
Precision Forming Process
The traditional forming method starts with large blocks of material to be cut into smaller blocks. In our proprietary process, the alloy material is first formed into a shape similar to the final product—thus reducing waste and cost. These savings we pass onto you, the customer.
Dy-free And Low-hre
dependence on HRE (Heavy Rare Earth) material used to control coercivity. Yunsheng has made enormous strides since 2012 to completely eliminate Dysprosium and Terbium from almost half our material grades. Today, Yunsheng already provides Dy-free grades up to 48H with significant HRE reductions (up to 70%) in our low-HRE grades. As Yunsheng anticipates the growing demand in Neodymium magnets from the automotive and industrial sectors for higher efficiency and cost-down opportunities, our R&D team continues to develop and expand its sustainable practices programme for HRE-free grades.
Material Grades
*For availability of Yunsheng grades, please contact your Yunsheng representative.
GRADE
(at 20°C) |
Br | Hcj | Hcb | (BH)max | Tw | ||||
T | kGs | kA/m | kOe | kA/m | kOe | kJ/m³ | MGOe | °C | |
N30 | 1.08-1.14 | 10.8-11.4 | 960 | 12 | 804 | 10.1 | 223-247 | 28-31 | 80 |
N33 | 1.14-1.19 | 11.4-11.9 | 960 | 12 | 843 | 10.6 | 247-271 | 31-34 | 80 |
N35 | 1.18-1.23 | 11.8-12.3 | 960 | 12 | 884 | 11.1 | 263-287 | 33-36 | 80 |
N38 | 1.23-1.28 | 12.3-12.8 | 960 | 12 | 915 | 11.5 | 287-310 | 36-39 | 80 |
N40 | 1.26-1.30 | 12.6-13.0 | 960 | 12 | 923 | 11.6 | 302-326 | 38-41 | 80 |
N42C | 1.29-1.33 | 12.9-13.3 | 960 | 12 | 915 | 11.5 | 318-342 | 40-43 | 80 |
N45C | 1.33-1.38 | 13.3-13.8 | 960 | 12 | 915 | 11.5 | 338-366 | 43-46 | 80 |
N48C | 1.38-1.42 | 13.8-14.2 | 960 | 12 | 915 | 11.5 | 362-390 | 46-49 | 80 |
N50C | 1.39-1.45 | 13.9-14.5 | 960 | 12 | 915 | 11.5 | 370-406 | 47-51 | 80 |
N52 | 1.43-1.48 | 14.3-14.8 | 960 | 12 | 875 | 11.0 | 390-422 | 49-53 | 80 |
N55 | 1.46-1.52 | 14.6-15.2 | 960 | 12 | 836 | 10.5 | 398-446 | 52-56 | 70 |
N58 | 1.49-1.55 | 14.9-15.5 | 876 | 11 | 836 | 10.5 | 422-462 | 53-58 | 70 |
N60 | 1.50-1.56 | 15.0-15.6 | 876 | 11 | 836 | 10.5 | 446-480 | 55-60 | 70 |
30M | 1.08-1.14 | 10.8-11.4 | 1114 | 14 | 812 | 10.2 | 223-247 | 28-31 | 100 |
33M | 1.14-1.19 | 11.4-11.9 | 1114 | 14 | 852 | 10.7 | 247-271 | 31-34 | 100 |
35M | 1.18-1.23 | 11.8-12.3 | 1114 | 14 | 883 | 11.1 | 263-287 | 33-36 | 100 |
38MC | 1.22-1.27 | 12.2-12.7 | 1114 | 14 | 915 | 11.5 | 287-310 | 36-39 | 100 |
40MC | 1.26-1.30 | 12.6-13.0 | 1114 | 14 | 940 | 11.8 | 302-326 | 38-41 | 100 |
42MC | 1.29-1.33 | 12.9-13.3 | 1114 | 14 | 964 | 12.1 | 318-342 | 40-43 | 100 |
45MC | 1.33-1.38 | 13.3-13.8 | 1114 | 14 | 995 | 12.5 | 338-366 | 43-46 | 100 |
48M | 1.37-1.42 | 13.7-14.2 | 1114 | 14 | 1019 | 12.8 | 358-390 | 45-49 | 100 |
50M | 1.39-1.45 | 13.9-14.5 | 1114 | 14 | 1035 | 13.0 | 370-406 | 47-51 | 90 |
52M | 1.42-1.48 | 14.2-14.8 | 1114 | 14 | 1035 | 13.0 | 386-422 | 49-53 | 90 |
55M | 1.45-1.52 | 14.5-15.2 | 1035 | 13 | 971 | 12.2 | 398-446 | 52-56 | 80 |
30H | 1.08-1.14 | 10.8-11.4 | 1353 | 17 | 820 | 10.3 | 223-247 | 28-31 | 120 |
33H | 1.14-1.19 | 11.4-11.9 | 1353 | 17 | 860 | 10.8 | 247-271 | 31-34 | 120 |
35HC | 1.17-1.22 | 11.7-12.2 | 1353 | 17 | 873 | 11.0 | 263-287 | 33-36 | 120 |
38HC | 1.22-1.27 | 12.2-12.7 | 1353 | 17 | 915 | 11.5 | 287-310 | 36-39 | 120 |
40HC | 1.26-1.30 | 12.6-13.0 | 1353 | 17 | 940 | 11.8 | 302-326 | 38-41 | 120 |
42HC | 1.29-1.33 | 12.9-13.3 | 1353 | 17 | 964 | 12.1 | 318-342 | 40-43 | 120 |
45H | 1.33-1.38 | 13.3-13.8 | 1353 | 17 | 1003 | 12.6 | 338-366 | 43-46 | 120 |
48H | 1.37-1.42 | 13.7-14.2 | 1353 | 17 | 1035 | 13.0 | 358-390 | 45-49 | 110 |
50H | 1.39-1.44 | 13.9-14.4 | 1353 | 17 | 1035 | 13.1 | 370-398 | 47-50 | 110 |
52H | 1.42-1.47 | 14.2-14.7 | 1274 | 16 | 1035 | 13.5 | 382-414 | 48-52 | 100 |
G55H | 1.47-1.52 | 14.6-15.2 | 1353 | 17 | 1106 | 13.9 | 414-446 | 52-56 | 120 |
G57H | 1.49-1.55 | 14.9-15.5 | 1353 | 17 | 1122 | 14.1 | 430-462 | 54-58 | 120 |
30SH | 1.08-1.14 | 10.8-11.4 | 1592 | 20 | 820 | 10.3 | 223-247 | 28-31 | 150 |
33SH | 1.14-1.19 | 11.4-11.9 | 1592 | 20 | 860 | 10.8 | 247-271 | 31-34 | 150 |
35SHC | 1.17-1.22 | 11.7-12.2 | 1592 | 20 | 873 | 11.0 | 263-287 | 33-36 | 150 |
38SHC | 1.22-1.27 | 12.2-12.7 | 1592 | 20 | 915 | 11.5 | 287-310 | 36-39 | 150 |
40SHC | 1.26-1.30 | 12.6-13.0 | 1592 | 20 | 940 | 11.8 | 302-326 | 38-41 | 150 |
42SHC | 1.29-1.33 | 12.9-13.3 | 1592 | 20 | 964 | 12.1 | 318-342 | 40-43 | 150 |
44SH | 1.32-1.36 | 13.2-13.6 | 1592 | 20 | 995 | 12.5 | 338-366 | 42-46 | 150 |
45SH | 1.33-1.38 | 13.3-13.8 | 1592 | 20 | 1003 | 12.6 | 342-366 | 43-46 | 150 |
48SH | 1.37-1.42 | 13.7-14.2 | 1592 | 20 | 1035 | 13.0 | 358-390 | 45-49 | 150 |
50SH | 1.39-1.44 | 13.9-14.4 | 1592 | 20 | 1043 | 13.1 | 366-414 | 46-50 | 150 |
52SH | 1.42-1.47 | 14.2-14.7 | 1512 | 19 | 1075 | 13.5 | 390-422 | 48-52 | 140 |
G55SH | 1.47-1.52 | 14.6-15.2 | 1592 | 20 | 1106 | 13.9 | 414-446 | 52-56 | 150 |
28UH | 1.04-1.09 | 10.4-10.9 | 1990 | 25 | 788 | 9.9 | 207-231 | 26-29 | 180 |
30UH | 1.08-1.14 | 10.8-11.4 | 1990 | 25 | 820 | 10.3 | 223-247 | 28-31 | 180 |
33UH | 1.14-1.19 | 11.4-11.9 | 1990 | 25 | 860 | 10.8 | 247-271 | 31-34 | 180 |
35UH | 1.18-1.23 | 11.8-12.3 | 1990 | 25 | 884 | 11.1 | 267-291 | 33-36 | 180 |
38UH | 1.23-1.28 | 12.3-12.8 | 1990 | 25 | 923 | 11.6 | 291-314 | 36-39 | 180 |
40UH | 1.26-1.30 | 12.6-13.0 | 1990 | 25 | 947 | 11.9 | 302-326 | 38-41 | 180 |
42UH | 1.29-1.33 | 12.9-13.3 | 1990 | 25 | 971 | 12.2 | 318-342 | 40-43 | 170 |
44UH | 1.33-1.36 | 13.3-13.6 | 1990 | 25 | 995 | 12.5 | 334-358 | 42-45 | 170 |
G45UH | 1.32-1.38 | 13.2-13.8 | 1990 | 25 | 995 | 12.5 | 338-366 | 43-46 | 170 |
G48UH | 1.36-1.42 | 13.6-14.2 | 1990 | 25 | 1027 | 12.9 | 358-390 | 45-49 | 180 |
G50UH | 1.39-1.44 | 13.9-14.4 | 1990 | 25 | 1051 | 13.2 | 374-406 | 47-51 | 180 |
G52UH | 1.42-1.48 | 14.2-14.8 | 1990 | 25 | 1067 | 13.4 | 390-422 | 49-53 | 180 |
G54UH | 1.45-1.51 | 14.5-15.1 | 1990 | 25 | 1090 | 13.7 | 406-438 | 51-55 | 180 |
28EH | 1.05-1.09 | 10.5-10.9 | 2388 | 30 | 788 | 9.9 | 207-231 | 26-29 | 200 |
30EH | 1.08-1.14 | 10.8-11.4 | 2388 | 30 | 820 | 10.3 | 223-247 | 28-31 | 200 |
33EH | 1.14-1.19 | 11.4-11.9 | 2388 | 30 | 860 | 10.8 | 247-271 | 31-34 | 200 |
35EH | 1.18-1.22 | 11.8-12.2 | 2388 | 30 | 884 | 11.1 | 267-291 | 33-36 | 200 |
38EH | 1.22-1.27 | 12.2-12.7 | 2388 | 30 | 923 | 11.6 | 287-314 | 36-39 | 200 |
40EH | 1.25-1.30 | 12.5-13.0 | 2388 | 30 | 947 | 11.9 | 302-326 | 38-41 | 190 |
42EH | 1.28-1.33 | 12.8-13.3 | 2308 | 29 | 971 | 12.2 | 318-342 | 40-43 | 180 |
G45EH | 1.32-1.38 | 13.2-13.8 | 2388 | 30 | 995 | 12.5 | 334-366 | 42-46 | 200 |
G48EH | 1.36-1.42 | 13.9-14.2 | 2388 | 30 | 1027 | 12.9 | 358-390 | 45-49 | 200 |
G50EH | 1.39-1.45 | 13.9-14.5 | 2388 | 30 | 1051 | 13.2 | 374-406 | 47-51 | 200 |
28TH | 1.05-1.09 | 10.5-10.9 | 2786 | 35 | 796 | 10.0 | 207-231 | 26-29 | 240 |
30TH | 1.08-1.14 | 10.8-11.4 | 2786 | 35 | 820 | 10.3 | 223-247 | 28-31 | 240 |
33TH | 1.14-1.19 | 11.4-11.9 | 2786 | 35 | 860 | 10.8 | 251-275 | 31-34 | 240 |
35TH | 1.18-1.22 | 11.8-12.2 | 2786 | 35 | 891 | 11.2 | 267-291 | 33-36 | 240 |
G38TH | 1.22-1.27 | 12.2-12.7 | 2786 | 35 | 931 | 11.7 | 287-310 | 36-39 | 240 |
G40TH | 1.24-1.30 | 12.4-13.0 | 2786 | 35 | 947 | 11.9 | 295-326 | 37-41 | 240 |
G42TH | 1.27-1.33 | 12.7-13.3 | 2786 | 35 | 963 | 12.1 | 310-342 | 39-43 | 240 |
G45TH | 1.32-1.38 | 13.2-13.8 | 2786 | 35 | 995 | 12.5 | 334-366 | 42-46 | 240 |
The above grades are our basic grades. We also have T and L-T series legacy grades which are derived from these basic grades,for example: N45T, 42MT, L-38SHT, L-38UHT. T and L-T series grades apply to those magnets which have low temperature coefficient and corrosion resistance requirements. The main properties of the derived grade such as Br, Hcj, Hcb and (BH)max correspond to those of basic grades. Additional performance data includes: µrec= 1.05 Basic grade: Tc = 310℃ αBr = -0.12 %/℃ вHcj = -0.70 %/℃ “T” grade: Tc = 330℃ αBr = -0.11 %/℃ вHcj = -0.60 %/℃ “L-T” grade: Tc = 350℃ αBr = -0.10 %/℃ вHcj = -0.50 %/℃
G” grades designate Grain Boundary Diffusion (GBD) grades using Yunsheng-patented technologies, without vacuum environment and reduced Heavy Rare Earth (HRE) content for Terbium (Tb) and Dysprosium (Dy).
|
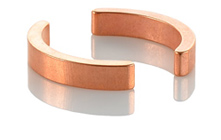